Upcycle House
In Nyborg, six single-family homes have been built under the name ‘the Mini-CO2 houses’. They are so named because they all seek to reduce the CO2 footprint of the construction through various environmentally sustainable strategies. The first house is designed by Lendager Group and is called ‘Upcycle House’.
86 % less CO2 has been emitted during the construction of Upcycle House than a classic single-family house of the same size. Moreover, all components of the house can be recycled after the end of their lifecycle and form part of new material cycles.
Resource Use
According to Lendager Group, the design of Upcycle House is based on an ambition to build a classic single-family house that can be disassembled at the end of its lifecycle so that the individual components of the house can be used in new material cycles. As the building and construction industries produce one third of all waste in Denmark, Upcycle House showcases how we can manage part of the waste problem if waste materials are used as a direct resource in the building. As the name indicates, most of Upcycle House is made of waste materials or useless products which have subsequently been upcycled and recycled.
Carbon Footprint & Lifecycle
A lifecycle analysis prepared by the Danish Building Research Institute in 2013 shows that Upcycle House emitted 86 % less CO2 in the construction phase than a reference house of the same size made from new materials. The explanation is that the materials used for Upcycle House ‘already paid the carbon bill’ when they were originally produced. The various upcycled materials used in Upcycle House include: Flooring consisting of cork and wood bi-products from furniture manufactures, insulation made of paper wool and glass shards from used glass as well as aluminium facade cladding made of recycled aluminium from beer and soda cans.
“We originally believed that the 65 % CO2 savings were unrealistic, but when we made calculations for the entire project, our CO2 account was actually 86 % better than a reference house. With that in mind, we are surprised that not everybody is working with this. Why is it not incorporated in everything we do as architects and why does the Danish Building Regulations not specify that a certain percentage of the building materials must be cycled?”, says Anders Lendager, Lendager Group, Realdania Byg 2014.
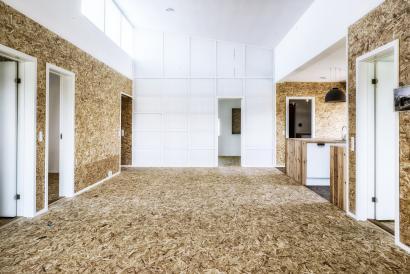
About the Case
In partnership with Realdania Byg, six different architectural firms have created six new single-family homes in Nyborg. The houses are called ‘the MiniCO2 Houses’ and, besides size and functional requirements, they all seek to reduce the carbon footprint by adopting various environmentally sustainable strategies.
The first house, ‘Upcycle House’, is made of waste materials or useless products which have subsequently been upcycled and recycled. The new materials developed for the house add a unique architectural expression. The house is a detailed and exciting example of the numerous opportunities that exist for recycling materials and reducing the carbon footprint of the building.